Breakdown of toner cartridge parts
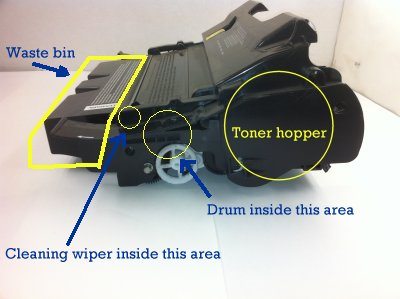
There are 2 main components in a toner cartridge, one is the toner hopper and the other is the waste bin.
Toner hopper:
- Magnetic Developer Roller – A cylindrical sleeve used to transfer image forming toner particles. The hollow cylinder is a non-magnetic material with a textured exterior surface. The interior contains a magnet producing a magnetic field to hold toner particles on the textured surface of the cylindrical sleeve.
- Doctor Blade – The Doctor Blade is a precise leveling blade which serves to keep toner on the Magnetic Developer Roller to a single layer. This is a critical component since any damage or maladjustment to the blade will produce a noticeable effect on the quality of the image.
- Sealing Blade – The Sealing Blade removes excess toner particles affixed to Magnetic Developer Roller as its outer surface rotates back into toner supply hopper and prevents toner particles from falling out of toner supply hopper onto paper along the length of developer sleeve.
Waste bin:
- OPC (Organic Photoconductor) Drum – A cylinder coated with a substance whose electrical properties change when exposed to light. The drum is electrically charged and a laser within the printer changes the electrical charge on areas of the drum. Those areas then pick up toner and transfer it to the page.
- Primary Charge Roller (PCR) – A rubber roller inside the toner cartridge which places the electrical charge on the Organic Photoconductor drum. It also erases the residual charge once the print cycle is complete.
- Organic Photoconductor Wiper Blade – The Organic Photoconductor Wiper Blade cleans the surface of the Organic Photoconductor Drum by scraping off the waste (untransferred) toner into the cartridge waste hopper.
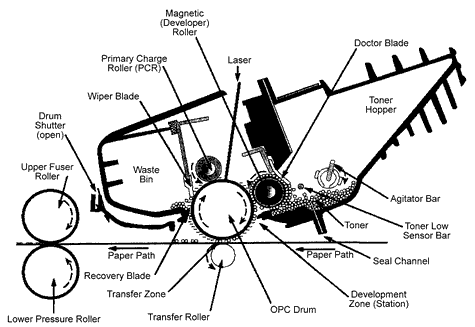
Print Cycle
The toner adder roller coats the developer roller with the toner (powder) while electrostatic-ally charging the particles with a negative charge. As the toner is deposited on the developer roller a leveling device called the doctor blade evens the toner applied to a thickness of approximately 15 microns. As the developer roller and the photo-conductor drum come in contact, the toner particles are pulled towards the charged electrostatic image on the photo-conductor drum.
Then when the paper passes under the drum the transfer roller applies
a slight electrical charge causing the toner to shift onto the paper
from the photo-conductor drum. The drum rotates up to two revolutions
per second timed with the exact speed of the paper ensuring a complete
transfer.
Next, the image is made permanent through a combination of precisely
controlled heat and pressure with the help of the fuser roller.
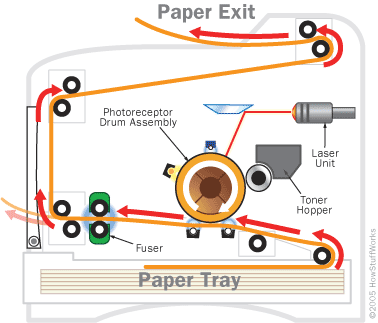
As the paper approaches the fuser roller which heats up to over 400 degrees (Fahrenheit) the applied toner on the paper reaches its melting point in just twenty three thousandth of a second and bonds onto the page under the roller pressure. The printed page is then ejected out of the printer. As the page is ejected the cleaning blade gently removes any stray particles of toner on the photo-conductor drum for the reception and printing of a new page; while the labelled image on the surface of the photo-conductor drum is erased by the Primary Charge Roller as it applies a new layer of negative charge on it.